FinVector’s new cleanroom facilities used to produce a unique gene medicine
5.5.2021 – A facility in Savo is the first in the world to produce a new cancer medicine. Finland’s leading cleanroom designers from Granlund Kuopio were responsible for the HVAC and cleanroom design of FinVector’s new manufacturing facilities.

FinVector, which specialises in the manufacturing of gene and antiviral medicine, has begun the manufacturing of a new medicine intended for the treatment of bladder cancer. The most important markets for the new form of treatment are in the United States, where the medicine’s patient tests are nearing completion. FinVector’s owner, Trizell Group, is currently applying for a sales permit for the medicine.
“We have known for years that the capacity of our existing cleanroom facilities is not high enough when aiming for commercial production”, says FinVector’s Planning, Procurement and Logistics Department Head Mikko Kämäräinen regarding the project’s background. The manufacturing of biological medicinal products is not easy to transfer from one location to another. In fact, the new cancer medicine cannot currently be manufactured anywhere else in the world. “We in Kuopio have unique expertise.”
Local cleanroom design and construction expertise
The new gene medicine’s manufacturing creates approximately 50 new jobs in Kuopio. FinVector also wished to use local expertise for design and construction. “We considered international designers that have experience with pharmaceutical companies, but once we looked at Granlund’s hospital design references, we decided to use the services of a local operator”, says Kämäräinen.
Local cooperation with the same designer from the concept design to the construction phase had many benefits. For example, the designers offered support in contractor selection and tender material preparation. “International companies do not have Granlund Kuopio’s local knowledge and networks that made it easy for us to find local contractors”, says Kämäräinen.
Completing the approximately 25-million-euro project on schedule requires sufficient resources, which were ensured through cooperation between Granlund and AINS Group. AINS Group was responsible for construction management and project management, while Granlund was responsible for cleanliness management and MEP monitoring.
“We got assistance whenever we needed it, meetings were arranged quickly and designers were easy to contact”, summarises Kämäräinen. A welcome addition to seamless cooperation was that Granlund’s Cleanroom Specialist, Mari Jäntti, had previous experience with FinVector’s cleanroom laboratory.
“I am familiar with FinVector’s manufacturing processes and the principles of working in cleanroom facilities, so the manufacturing facility’s operations could be taken into account from the beginning in the design”, says Jäntti. Kämäräinen is also grateful for this. “Communication was smooth in the concept-phase workshop, and it seemed like everyone was on the same page.”
Cleanroom facilities designed for an existing building
The nearly 800-square-metre cleanroom facilities were designed for a space that previously housed office and laboratory spaces in Kuopio’s Technopolis. One challenge was fitting demanding technology into an existing building.
Cleanroom design is always special construction, where HVAC and building automation design is used to ensure the management of air current directions, room pressures, temperatures, moisture and particles”, Jäntti explains. “The cleanliness and room pressure differences achieved with efficient ventilation must be maintained to prevent cross-contamination.”
Granlund also takes care of the manufacturing facilities’ equipment, fixture and layout design. For example, the different spaces required air locks between them. The electrical design also accounted for the hygiene requirements of a cleanroom. “We aimed to integrate all lighting fixtures and sockets into the walls”, says Jäntti.
Knowledge of European and US cleanroom standards
The design of the new manufacturing facilities accounted for both the European GMP cleanroom classification system and the US’s FDA regulations. The required English language validation documentation and testing were exceptionally strict. Quality could not be compromised.
“The designers of a pharmaceutical goods manufacturing facility must know what they are doing and produce high-quality documentation as part of our quality system”, says Kämäräinen.
The new facilities were completed last summer. The first year has involved installing process devices, carrying out validations and making test batches. “One of the most important things has been ensuring the correct functionality of the ventilation system, which ensures biosafety. The facilities’ exhaust air is also filtered”, Jäntti explains.
The facilities have been well-received. “Our manufacturing representatives participated in the design of the facilities, so our employees have been able to use the new facilities smoothly from the start. The equipment works as planned”, says Kämäräinen.
Would you like to hear more?
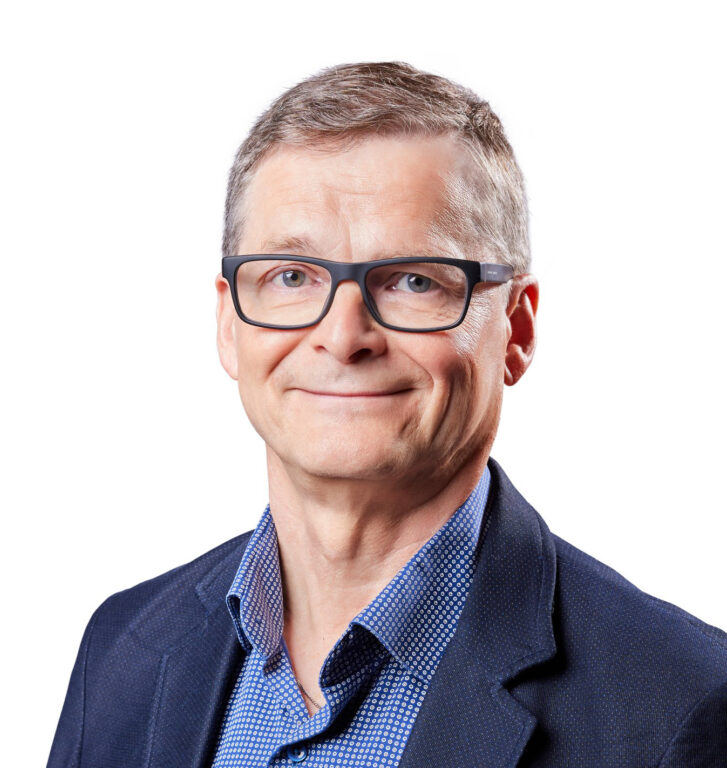